Our CareA spray-type adhesion barrier
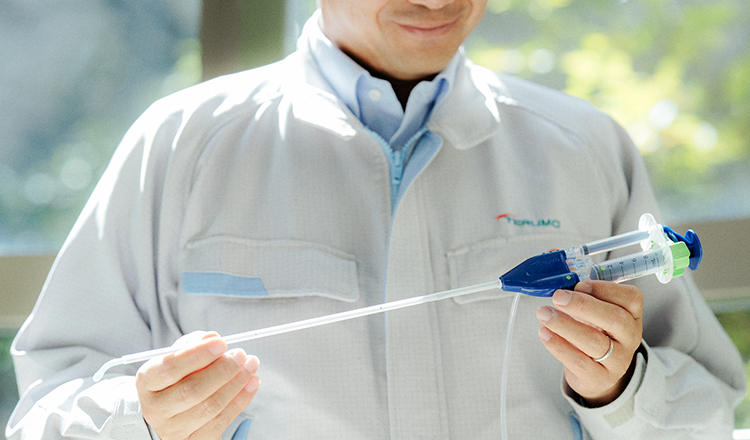
“We aspire to create products that meet the needs of medical settings”
“We aim to improve the quality of life of patients undergoing surgical treatment”
— These were the driving forces behind this development project.
A spray to address the clinical issue of postoperative adhesions
When tissue is lost or damaged during surgery, etc., a phenomenon known as postoperative adhesions may occur during the healing process. In this process, organs and tissue surfaces that are normally separated become connected, and there have been many reports on the clinical issues it poses and responses.
For example, The European Society for Gynecological Endoscopy (ESGE) summarized its views on the current situation in 2022 in ‘The Future of Adhesion Prophylaxis Trials in Abdominal Surgery: An Expert Global Consensus’. At the beginning of the report, postoperative adhesions are described thus; ‘Indeed, abdominal and pelvic surgeries are the most common cause of peritoneal adhesions and remain a source of considerable morbidity.’*1
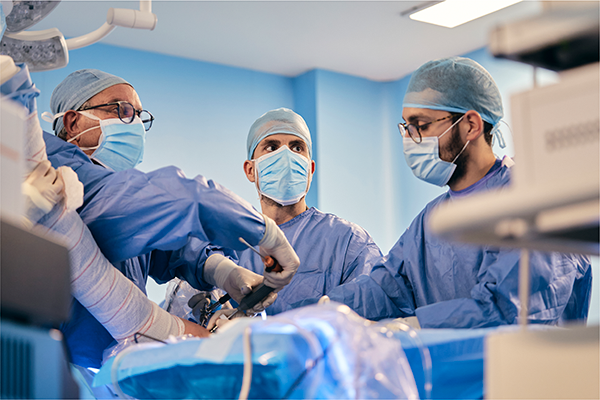
Physical barriers can be used as medical devices as a means to reduce these postoperative adhesions, and various types of products and developments such as solutions, hydrogels, solid membranes and films have been reported around the world.*2
After many years of searching for the relevant requirements, and advancing research and development, Terumo developed AdSpray, an adhesion barrier applied as a spray that forms a hydrogel on the target tissue. AdSpray was approved as a medical device by PMDAin 2016, first launching the product in Japan.
-
*1
De Wilde, R.L., Devassy, R., Broek, R.P.T., Miller, C.E., Adlan, A., Aquino, P., Becker, S., Darmawan, F., Gergolet, M., Habana, M.A.E. and Khoo, C.K., 2022. The future of adhesion prophylaxis trials in abdominal surgery: an expert global consensus. Journal of Clinical Medicine, 11(6), p.1476.
-
*2
Tang, J., Xiang, Z., Bernards, M.T. and Chen, S., 2020. Peritoneal adhesions: Occurrence, prevention and experimental models. Acta biomaterialia, 116, pp.84-104.
Support from many physicians helped push development forward
“At first there wasn’t a business division. We took up the constituent technologies of senior engineers who were trying to solve the issue of adhesion barrier materials, and everyone on the team was searching for something better,” explains Naotaka Chino who was the material designer and development manager at the time.
So why choose a spray-type adhesion barrier when there were so many different materials available? Chino looks back at how the idea got started.
Chino: “The idea of a spray-on adhesion barrier was our senior engineers’ idea.
During the early stages of investigation, we knew that laparoscopic surgery was gaining popularity as a minimally invasive surgery in Japan. In addition, adhesion barriers can be used not only on the flat area under the abdominal incision, but also on various areas that follow the structure and shape of the target organ.
There was therefore a need to develop a highly malleable adhesion barrier that could be attached to the complex shapes of tissue surfaces, and which would allow easy access to the treatment site regardless of the surgical procedure.
To further flesh out these ideas, the engineers visited academic conferences and hospitals, and gathered opinions from many physicians.”
Miho Kai, who was in charge of product evaluation and usability, continues:
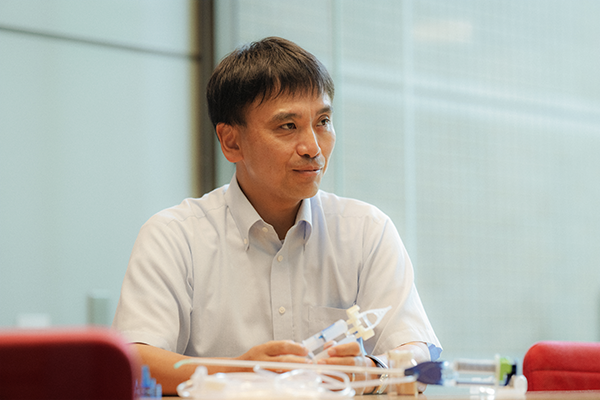
Kai: “Adopting a spray-on format barrier was an idea that 10 out of 10 people would say ‘would be good’. I still remember a pediatrician telling me that he wanted an adhesion barrier suitable for the small bodies of children to be available on the market.”
This encouragement from physicians made the team really feel that they would be able to solve a range of medical issues and help save patients. The team became driven by a strong desire to succeed in developing the product no matter what it would take.
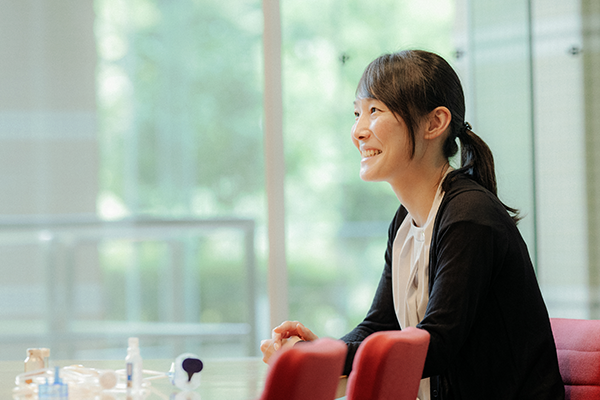
Terumo developed everything from the ground up, from the main ingredient to the device.
This made it possible to achieve an effective spray-type adhesion barrier.
Kai: “We spoke to gynecologists. All of them were in favor of the idea, and some even agreed to participate in our experiments, so we were really determined to incorporate their voices into the finished product.”
This adhesion barrier was developed based on the concept of ‘a spray-type, easy-to-use adhesion barrier.’ This is a rare product even for Terumo, as everything from the main ingredient to the device was developed in-house. As a result, there were many challenges that had to be overcome in the course of the product’s development.
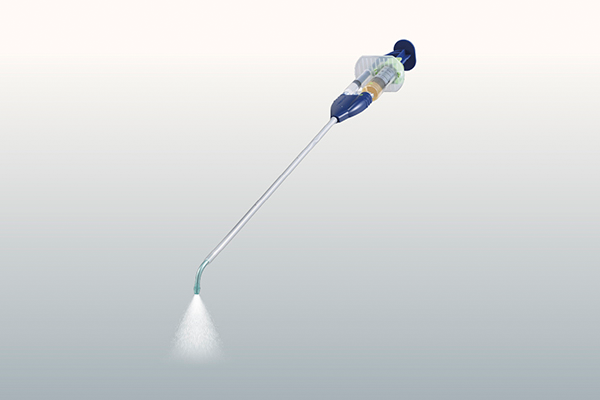
Chino: “This product was the first to be developed entirely at Terumo’s Shonan Center, including everything from the main ingredient to the materials for the device. Even stable reproduction of the patented ingredients was very difficult at that time.”
The reason for this was that, during use, the powdered ingredients are dissolved and sprayed, but when the rainy season arrived and humidity levels increased, it became virtually impossible to effectively manufacture the powder. Perhaps due to these conditions, some of the powder dissolved and some did not, making it extremely difficult to ensure the homogeneity of the product. Each time team members faced difficulties, they adjusted the humidity and temperature of the equipment, changed the mix of materials used in the powder, optimized testing parameters, and came up with ideas.
Kai: “The fact that many members of our team had knowledge of pharmaceuticals also helped with the process of mass-producing the main ingredient.”
Because we chose a unique spray-type barrier, we had to design and manufacture a huge number of materials and parts for the device. In search of the optimal solution for the device’s construction, engineers worked closely together to complete many of the parts, but hurdles remained.
Since manual assembly was the best way to put together the vast number of components, the team also built its own more rigorous inspection system.
In the end, it took seven years to scrutinize the basic technology and five years from development to mass production, to successfully commercialize the product.
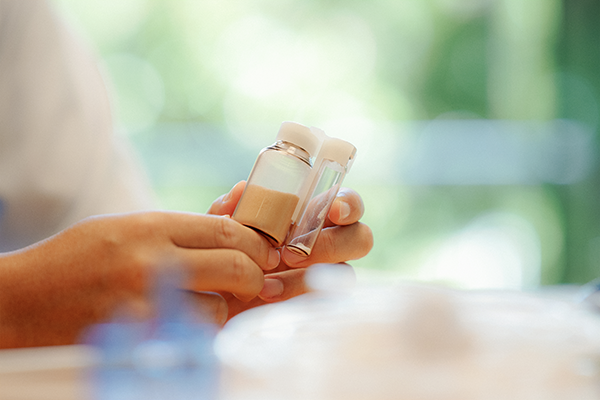
Through multiple rounds of trial and error, the team members repeatedly discussed the requirements for the spray-type adhesion barrier, and found this product to have four advantages, namely excellent biocompatibility, a hydrogel that can be applied to complex surgical areas, accessibility suitable for laparoscopic surgery, and excellent visibility enabling confirmation even during endoscopic surgery. Terumo was able to introduce an adhesion barrier product with these features to the Japanese market, the country in which it was developed.
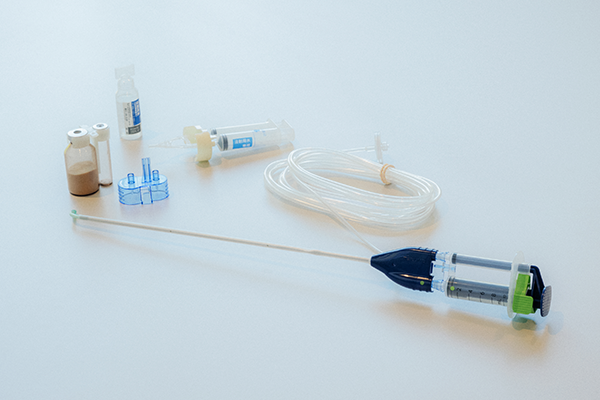
An all-Terumo adhesion barrier developed from scratch.
Passing on the experience of this success to the next generation.
Chino: “How to come up with ideas to solve medical issues is important to developing medical devices. Effectively delivering those ideas to the world requires the people who make and deliver products to be highly motivated. I want for us to keep this in mind as we work on development in the future.”
Kai: “It’s very rare in product development to go from initial development all the way to mass production. I’d like to utilize this experience of success creating an all-Terumo product in future. I’d also be delighted if it motivates our employees in departments like sales and our junior staff.”
Chino: “I’d like for us to respond to the voices within the company saying, ‘this product should be released not only in Japan, but also in the U.S. and other countries.” I’d also like to consider promoting more broadly the advantages of Terumo’s capability to manufacture everything from medical devices to pharmaceuticals in bulk.”
This product was developed as a result of the team and its predecessors’ passion and technologies, in order to reduce the risk of complications after surgery. Terumo will continue to develop this product to further refine and enhance it, in order to help solve other medical issues.
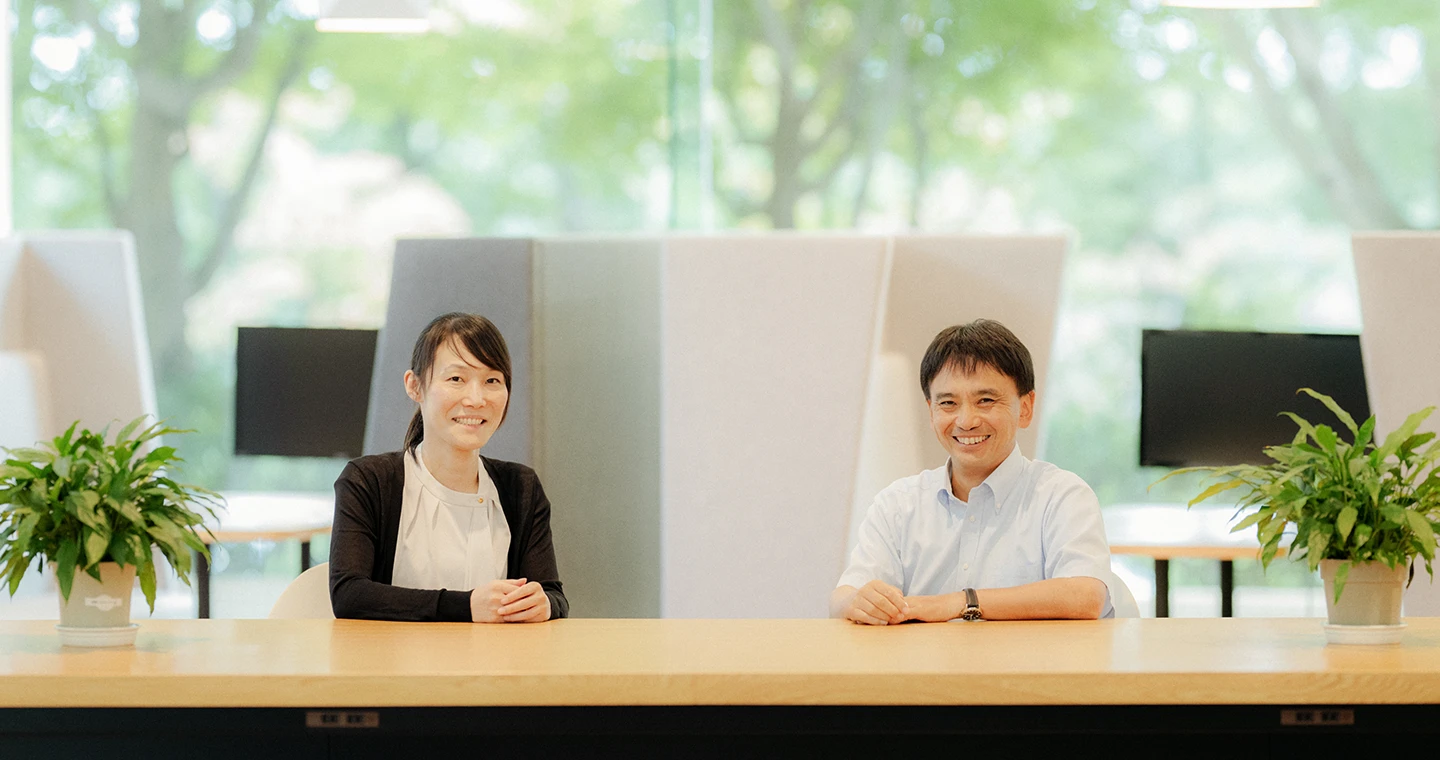
Profile
Naotaka Chino
Joined Terumo in 2006.
Joined AdSpray’s development team and led it as a development manager, involved from the feasibility stage until launch. Since then, he has been in charge of creating new themes and new developments in the digital field.
Miho Kai
Joined Terumo in 2008.
Joined AdSpray’s development team and was involved from the feasibility stage until launch. Since then, she has been in charge of new developments in the biosurgery field.
Technologies & Solutions
Spray-type Adhesion Barrier
Easily sprayed to exactly where you need it.
A spray-type adhesion barrier with nozzle applicator.
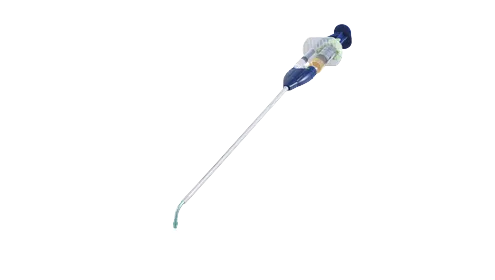