Our Care3D-Shin
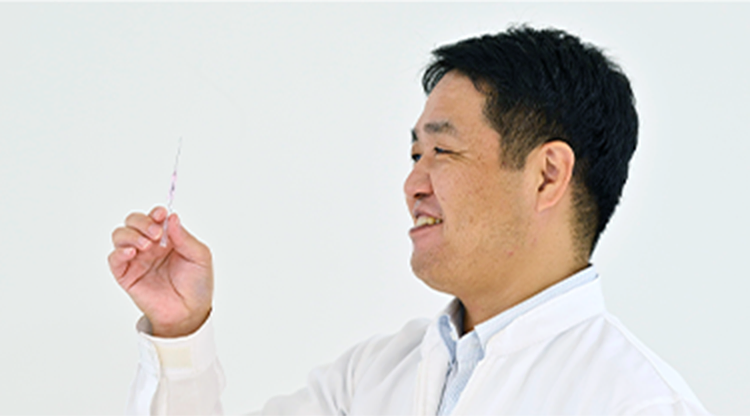
The psychological burden of needle insertion weighs heavily on both patients and healthcare professionals.
When our engineers learned this, we decided to find a way to reduce the burden on both the patient and the professional.
“Ensuring the needle finds its mark, regardless of age or gender.”
Technology developed from the ground up to achieve successful insertion on the first try.
Vascular needle insertion is a very basic act in the medical field. Yet it requires a high level of skill to insert a needle accurately into the desired area. For patients, needle insertion is often accompanied by fear and pain.
Needle reinsertion, which can vary on the patient’s physical characteristics and the healthcare professional’s experience, imposes a burden on the patient, but also a heavy psychological burden on healthcare professionals. Terumo regarded this as a medical challenge, and therefore embarked on the development of a needle that finds its mark on the first attempt.
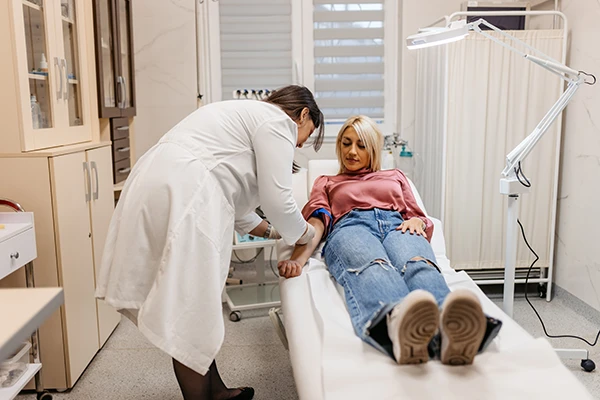
Daisuke Hosokawa has been involved in the development of infusion products for many years, and was in charge of developing needle-processing equipment for the 3D-Shin (shin means needle in Japanese). He describes his thoughts when he heard about the issue.
Hosokawa: “While talking with young medical professionals, I learned that they were very nervous about giving injections—They didn’t want to impose a burden on patients. That’s why I wanted to develop a needle tip that achieves access to the blood vessel with a single insertion, reducing the burden on both healthcare professionals and patients.”
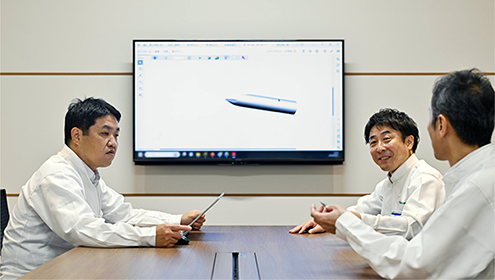
Masahiko Nagasawa, who has been involved with cannula products since joining Terumo, looks back on when he became responsible for overseeing development.
Nagasawa: “I was sure that Terumo, with its deep knowledge and experience in hypodermic needle technology, could develop a solution for this. ‘A needle that finds its mark, regardless of age or gender.’ To achieve it, we needed the needle tip to be the world’s sharpest. I was confident we could pull it off.”
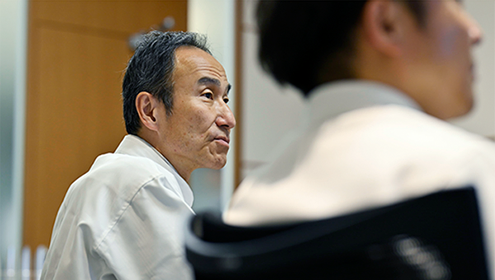
A unique shape that combines a short bevel and sharp tip angle.
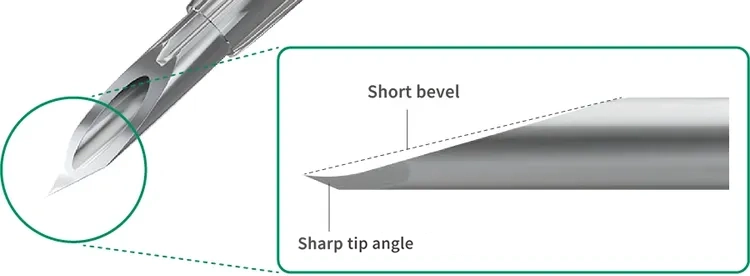
The secret of the high insertion accuracy of the 3D-Shin comes from the Terumo’s unique combination of a short bevel and a sharp tip angle.
Nagasawa: “If the needle tip is not sharp enough, it will slip on the blood vessel and you will not be able to insert it on the first attempt. So the angle and sharpness of the needle tip are very important.”
Hosokawa: “The sharpness of the needle tip alone is not enough. We spent a lot of time deciding the shape of the entire bevel so that it can be inserted into blood vessels smoothly.”
The engineers improved the sharpness to increase ease of insertion, and in order to reduce insertion resistance, the needle tip angle was made sharper than the conventional model. The bevel length was also shortened to prevent the needle tip from penetrating the blood vessel wall in the event the needle tip misses the center of the blood vessel during insertion.
Nagasawa: “If this sharpness makes it possible to insert in one attempt, it not only reduces the burden on patients and healthcare professionals, but also reduces the number of needles used, which has the benefit of being kind to both medical economy and the environment.”
Taking on the challenge of a novel processing technology that achieves two technologies that are difficult to balance
Achieving both a short bevel and a sharp tip angle on a thin hypodermic needle was no easy task. It took about eight years of ground-up thinking and prototypes to achieve the ideal performance, from selecting the material and bevel shape to the grinding method.
Hosokawa: “When it comes to how we sharpen the needle tip, conventional methods aren’t enough. So we had to start from zero and develop everything from scratch.”
Takashi Chubachi, an engineer who has been working hard to improve the production technology explains:
Chubachi: “I was so focused on the needle tip’s insertion resistance, I ended up increasing the maximum resistance of the needle overall. Even if the insertion resistance was ideal in theory, it didn’t work well when we tried to pierce skin-like material.”
Going about it this way, we amassed an enormous number of 3D CAD and prototypes before the product was completed.
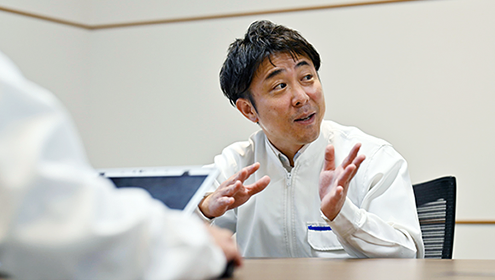
Nagasawa: “There were also limitations to mass-producing this needle shape using existing processing methods.”
Chubachi: “In order to make possible the special processing needed, we had dramatically change our mindset to simultaneously develop equipment.”
As the two engineers explained above, the 3D-Shin could not be manufactured using the general processing method employed for regular hypodermic needles, which are formed from three planes. The current manufacturing facility was achieved having investigated new processing methods. Not only the equipment, even the grindstones used to sharpen hypodermic needles needed rethinking. It was necessary to consider the balance between reliable quality and manufacturing cost from among countless grindstones. We ultimately arrived at an ideal balance in cooperation with a grindstone manufacturer.
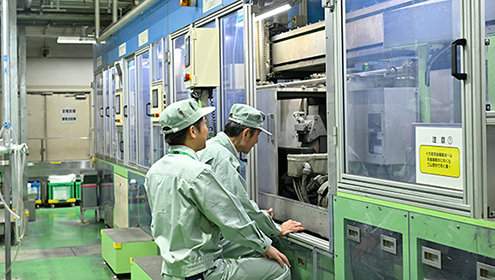
The first attempt extended to quality inspection and uniformity in mass production. Mass-producing an unprecedented tip shape requires precise manufacturing control. There were numerous issues, such as the strength of the retaining force of the pipe jig when creating the tip, and how to inspect the needles. The 3D-Shin is a groundbreaking hypodermic needle for Terumo, which undertook everything from development to inspection and mass production, all entirely from scratch.
The potential of the 3D-Shin discovered via feedback from medical settings.
The 3D-Shin overcame extremely difficult development and mass-production challenges. Chubachi comments that he was encouraged by the positive feedback he received about the needle’s performance.
Chubachi: “When we demonstrated it at an academic conference, one doctor was so surprised, asking, ‘Is it already in the vein?’”
It’s hoped that patients who previously needed two or more attempts to access a blood vessel will now require only one attempt, and that insertion into the thin blood vessels of elderly people can be achieved more reliably.
It’s also hoped that it will allow smooth insertion into arteries with arteriosclerosis or calcification, as the needle can be seen clearly via ultrasound even during insertion.
This is a product filled with the passion of Terumo’s engineers.
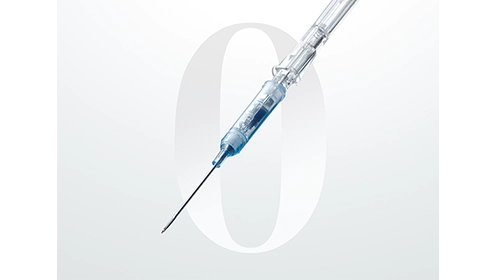
The 3D-Shin is used in the arteriovenous
indwelling needle “Surflo ZERO”.
Going beyond boundaries to create a future that benefits more people
The name ‘3D-Shin’ was chosen through an internal competition. It expresses our pride in the fact that it is an hypodermic needle with a high degree of freedom. Each member of the development team shared their thoughts about the future of the 3D-Shin.
Nagasawa: “I’d like this product to become so widespread that people will say, ‘If you want to inject into a vein, use a 3D-Shin.’ I’d like it to be of benefit to as many patients and healthcare professionals as possible.”
Chubachi: “I hope that this needle will be adopted not only in Terumo products, but also in a variety of products outside of the company. I think that through co-creation, we can deliver these benefits to healthcare professionals and patients in a broad range of fields that Terumo has not yet expanded into.”
Hosokawa: “I’d be happy if the world recognizes that Terumo needles are reliable, and that they can be used not only in healthcare but also in other fields such as research and pharmaceuticals.”
Terumo’s hypodermic needle technology continues to focus on reducing both physical and psychological burdens. With our innovative technology, we will continue to contribute not only to patients’ well-being, but also to medical settings, research, pharmaceuticals, and other fields.
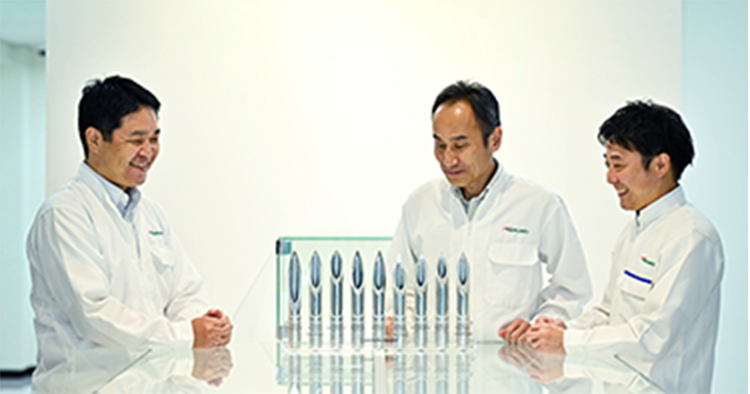
Terumo's unique "3D-Shin" technology
- An insertion needle that incorporates two shape elements, using unique technology that aims to improve the success rate of insertion -
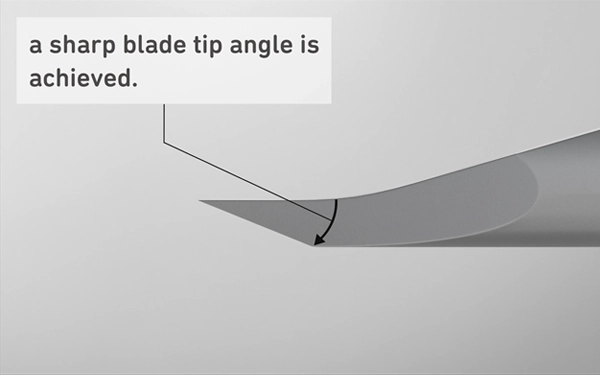
-
*
Your name and e-mail address are required for watching videos
Profile
Daisuke Hosokawa
Joined Terumo in 1995.
After his involvement in the development of mass-production equipment for infusion products, he went on to join the 3D-Shin development team in 2016. He has learned how to make cannulas effectively from scratch.
Masahiko Nagasawa
Joined Terumo in 1981.
Long involved in the development of cannula-related production equipment and production technology, he has also been responsible for the development and prototype production of new cannula shapes. He has spent 43 years devoted to cannulas.
Takashi Chubachi
Joined Terumo in 2004.
Involved in the development of mass-production equipment for indwelling needle products and cannula-related products, he participated in the launch of mass production of the 3D-Shin in 2015. He is passionate about utilizing his experience with general cannulas to contribute to the 3D-Shin.
Technologies & Solutions
Short bevel and sharp tip angle
An hypodermic needle that incorporates two shapes, using unique technology that aims to improve the insertion success rate.
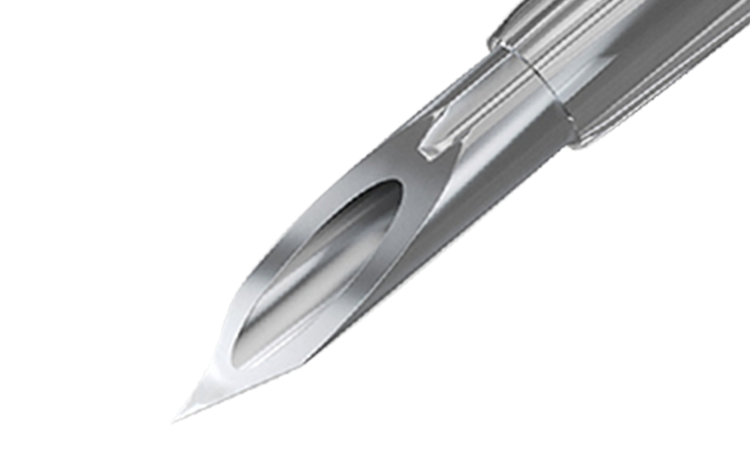